이번에는 저번의 식각공정에 이은 증착공정이다. 이것이 보편적인 방법인지는 모르겠으나, 본인이 들었던 반도체 8대공정 강의들은 증착공정을 먼저 소개하고 그 다음 식각, 뒤이어 포토공정의 순으로 구성되어 있는 것이 대부분이었다. 그러나 엔지닉 반도체 스터디 강의에서는 포토를 먼저, 그 다음 식각과 증착으로 구성되어 있는데, 지금이야 괜찮지만, 과거의 본인이 이런 순서로 반도체 공정을 배웠다면 플라즈마 공정을 보다 쉽게 이해할 수 있지 않았을까 하는 생각이 든다. (본인은 반도체 공정을 처음 배울 때, 플라즈마 증착공정과 식각공정의 이해에 많은 어려움을 겪었다.)
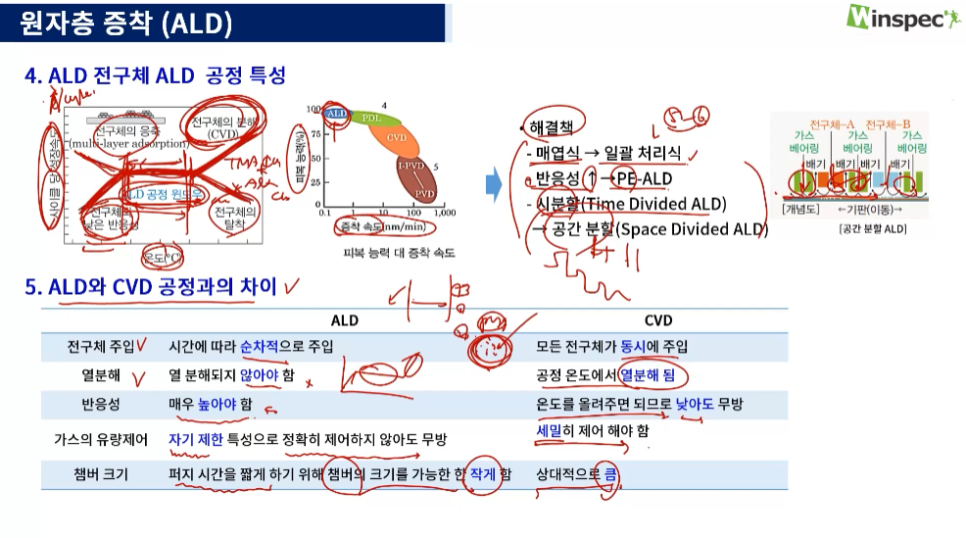
CVD 공정은 기체 상의 Precursor의 화학 반응을 이용하여 웨이퍼의 표면에 고체 상의 Thin Layer를 증착하는 방식이다.
물리적 성향을 띄는 Sputter Etch와 화학적 성향을 띄는 Plasma Etch의 비교에서 Sputter Etch는 Selectivity가 낮고, Plasma Etch는 Selectivity가 높았던 것과 같이,
CVD 공정은 물리적으로 증착하는 PVD의 방식보다 Conformal한 성장이 좋다.
따라서, 현재 PVD는 주로 CVD Precursor를 구하기 어려운 금속과 같은 물질의 증착에만 사용된다.
(이 또한 소자 미세화가 진행될수록 결국에는 CVD로 변경될 가능성이 크다.)
CVD에는 상압에서 반응을 진행하는 APCVD와, 저압(진공)에서 반응을 진행하는 LPCVD, 플라즈마를 사용하는 PECVD로 구성된다.
CVD는 산화막 성장에서 그랬듯이, 반응속도 결정 단계에 따라 Mass Transfer Limited Region과 Surface Reaction Limited Region으로 구성된다.
기체 상의 분자나 원자의 확산은 표면 반응보다 온도에 덜 의존하기 때문에 온도에 따른 변동이 적다.
그 말인 즉슨, 온도가 조금 변했다고 증착 속도가 크게 변하지 않는다는 뜻이다.
(제조업의 매우 중요한 요소 중 하나는 Uniformity로 더도 말고 덜도 말고 설계 과정에서 예상하고 기대한 그대로 결과물이 나오는 것을 원한다!)
(매우 중요하니 두 번 말하고 싶다!)
그렇기에 과거에는 온도 Control을 그렇게 엄격하게 할 필요 없는 APCVD가 이용됐지만, APCVD에는 치명적인 단점이 존재했다.
Precursor가 너무 많아지면, 표면이 아닌 공중에서 Precursor끼리 반응해 버린 반응생성물 (Particle) 따위가 웨이퍼 표면에 붙어 막질을 낮출 수 있다.
그리고 무엇보다도, Mass Transfer Limited Region이기 때문에 Precursor의 유동을 Reactor 내의 모든 웨이퍼에 동일하게 맞춰야 한다.
이 소리는 무엇이냐면, 어떤 웨이퍼에 Precursor 가스가 많이 가고 어떤 웨이퍼에는 Precursor 가스가 그것보다 더 적게 가고 이러면 안 된다는 소리이다.
APCVD는 Reactor 내에 Laminar Flow로 가스를 주입하는데,
이때 가스 흐름과 웨이퍼 사이의 Boundary Layer는, 가스 주입부에 가까운 웨이퍼의 것이 멀리 떨어진 웨이퍼의 것보다 더 두꺼운 영향을 갖는다.
당연히 이 Boundary Layer의 차이는 웨이퍼 간의 증착속도를 다르게 하는 요인이 되는데,
APCVD에서는 SiC Susceptor 따위를 투입해서 뒤쪽 웨이퍼의 얇아진 Boundary Layer를 상대적으로 높이 위치시킴으로 그 차이를 열심히 보정하고 있다.
물론 그래도 높은 Uniformity를 달성하기 힘들고, 이런 이유 때문에 한 Reactor 내에 웨이퍼를 많이 넣기도 곤란하다.
그러니 업계 관계자들은 이런 생각을 하게 된다.
'아니 온도 컨트롤 힘들 거 같어서 APCVD 하는 건데, 이럴 바엔 그냥 온도 컨트롤 하는 게 더 쉽겠다!'
그렇게 등장한 것이 LPCVD.
LPCVD는 Reactor는 저압의 Surface Reaction Limited Region에서 진행된다. (APCVD보다 높은 온도에서 진행된다.)
앞서 말했듯이 표면반응의 속도는 온도에 민감하기 때문에 LPCVD는 엄격한 온도 Control이 가능한 Hot Wall Reactor에서 진행된다.
LPCVD는 APCVD와 다르게, 저압에서 진행되기 때문에 증착속도가 낮다.
(Precursor Gas의 양은 곧 압력임을 유념한다.)
그러나, 이 단점은 Batch 방식을 도입함으로 해결할 수 있다.
Precursor의 유동은 LPCVD에서 별다른 영향을 끼치지 못하기 때문에, Susceptor를 넣을 필요도 없고 APCVD 때보다 걱정없이 웨이퍼를 우겨넣을(?) 수도 있다.
이러니 LPCVD의 압승이 아니겠는가.
물론 LPCVD에서도 결국에는 Precursor 가스가 웨이퍼에 표면에 붙어서 표면반응하는 것을 이용하는 방식인 이상, Precursor 가스의 유동의 영향을 받지 않을 수가 없다.
LPCVD의 이러한 문제는 Aspect Ratio가 큰 부분의 증착과정에서 매우 잘 드러나는데,
DRAM의 Capacitor와 같이 Aspect Ratio가 매우 큰 곳은 LPCVD를 진행해도 만족스러운 수준의 Step Coverage를 얻기 힘들다.
이러한 문제를 해결하기 위해 인류는 궁극의 Step Coverage를 갖는 증착 방식을 생각해냈으니,
그것의 이름은 ALD이다.
ALD는 Atomic Layer Deposition으로 이름부터 끝판왕 보스와 같은 느낌을 풀풀 낸다.
Atomic Layer의 이름에서 볼 수 있듯이, ALD는 원자층 수준으로 박막을 증착하는 것이다.
'아니 그게 가능하다고? '
예 가능합니다. 이러한 증착은 Chemisorption과 Physisorption 간에는 큰 에너지 차이가 존재하기에 가능하다.
갑자기 뜬금포로 용어가 나와서 당황스러울 수도 있지만,
Chemisorption은 화학반응과 같은 것으로 Chemical Bonding이 이루어진 것이고
Physisorption은 단순히 Van Der Waals Forces나 London Dispersion Forces와 같은 쌍극자 힘에 의한 인력으로 이루어진 것이다.
당연히 Chemical Bonding 쪽이 후자와 같은 힘들에 의한 결합보다 압도적으로 더 방출되는 에너지가 크기 때문에 더 안정하다고 말할 수 있다.
그렇다면 반대로 이 결합을 끊는다고 생각해보자.
생각할 필요도 없이 더 강하게 결합된 Chemical Bonding을 끊는 것이 더 힘들 것이다.
ALD는 바로 이것을 이용한 것이다.
ALD에서는 일단 진공의 Reactor에 Precursor를 공급한다.
어느 정도로 공급하냐면, 아까 말했던 Atomic Layer 따위는 그냥 생각치도 말고 아주 증착하고자 하는 Hole을 거의 메꿔버릴 정도로 공급해버린다.
Hole이 Precursor로 다 메꿔져 망했다고 생각할 찰나, N2와 같은 반응성이 낮은 Gas를 주입하고 이를 강하게 펌프로 배기시킨다.
그렇다면 웨이퍼의 표면에 붙은 Precursor도 떨어져 나갈 텐데, 펌프의 힘이 너무 쎈 나머지 거의 대부분이 홀랑 떨어져 나가 버린다.
그러나, 이때 웨이퍼 표면과 직접적으로 닿아있는 첫 번째 Precursor 층은 Chemisorption을, 나머지는 Physisorption을 하고 있기 때문에
강하게 결합되어 있는 첫 번째 Layer를 제외한 나머지 Layers가 떨어져 나가 버린다.
축하합니다. 단 한 층의 Layer를 웨이퍼에 붙이는 데에 성공했습니다.
그러나 이게 끝이 아니다.
ALD는 CVD와 같이 반응 참여물 즉, Precursor Gas들을 한번에 공급하는 것이 아닌 순차적으로 공급하는 방식이다.
그러니까, H2와 O2 반응이 있다면 우리는 H2만 넣은 셈이고, 지금까지의 과정은 절반만 ALD를 진행한 격이다.
첫 번째 Layer의 증착에 성공했다면 반응에 참여하는 Precursor를 첫 번째 Layer와 똑같은 방법으로 증착시킨다.
이때 첫 번째 Layer에는 두 Precursor가 만나 표면 반응이 이루어질 테고, Precursor를 각각 단 한 층씩 증착시켰기 때문에,
다른 Precursor까지 증착을 마쳤다면 단 한층의 반응물 층이 Wafer에 붙어있을 것이다.
우리는 이 과정을 ALD의 한 Cycle이라고 부른다.
ALD의 한 Cycle이 1초든 1분이든 1시간이든, 결국에는 단 한 층의 Layer가 웨이퍼에 붙어있을 테니
더이상 ALD의 진행 시간은 Deposition Rate에 아무 영향을 미치지 못한다.
(물론 당연히 생산성은 ALD 시간이 길수록 낮으니까 ALD 진행 시간은 짧을수록 좋다.)
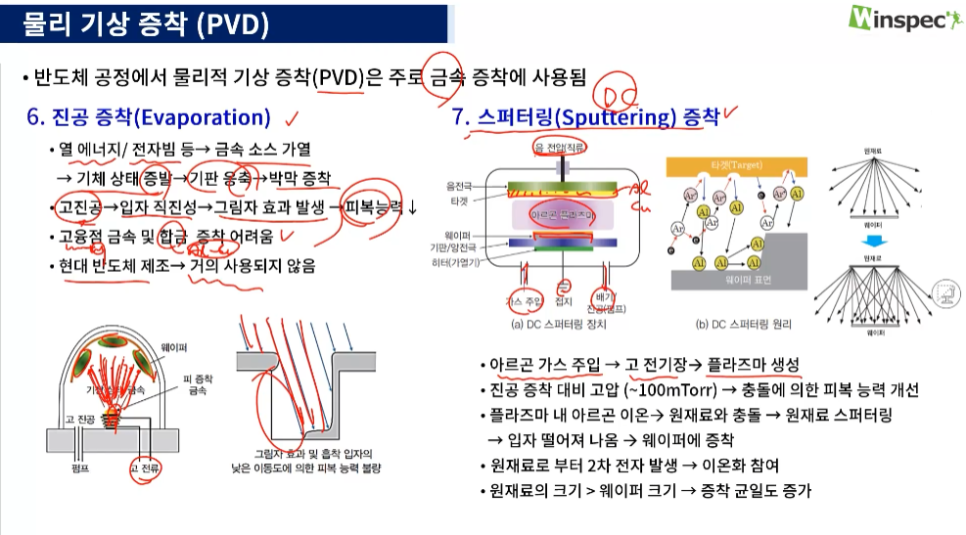
이번에는 Evaporation에 대해 이야기 해보겠다.
Evaporation은 현대 반도체 제조에서 사용되지 않는 방법으로 이유는 다음과 같다.
Evaporation은 말 그대로 Target 물질에 고 에너지를 가해 원자나 분자가 Chamber 내에 부유하는 형태로 만들고 그것을 상부의 웨이퍼에 증착시키는 방식이다.
이러한 방식 때문에 PVD와 비슷하게 Uniformity가 낮다.
그렇다고 고진공을 증착시켜 Mean Free Path를 늘려 직진성을 향상시킨다면 이번에는 웨이퍼의 구조에 가려져서 일부 지역이 상대적으로 낮은 Deposition Rate를 보이는 Shadow Effect가 나타난다.
그리고 합금을 증착하고자 하는 경우, 각 금속의 Melting Points가 상이하기 때문에 별개의 Crucible에 각각의 물질을 Evaporate시켜야 하는데
이때 온도를 Control하는 것이 매우 힘들 뿐더러 생각한대로 잘 진행되지도 않는다.
또한 열의 형태로 Target 물질에 에너지를 가할 경우, Crucible의 입자가 같이 불순물로 섞여 들어갈 가능성이 있다.
이를 해결하기 위하여 E-Beam을 국부적으로 Target 물질의 표면에 가해 불순물의 혼입을 막는 E-Beam Evaporation이 있지만
여전히 Evaportation 방식이라는 것으로부터 기인하는 내재적인 문제점이 존재한다.
이러한 문제들 때문에 Evaporation은 거의 PVD와 CVD로 교체되었으며 디스플레이 쪽에서나 주로 쓰이는 방식이 되었다.
데일리미션
Q1. ALD공정과 CVD공정의 차이점에 대해 정리해보세요.
CVD 공정은 여러 종류의 Precursors를 동시에 주입하여 웨이퍼 표면에서의 반응을 통해 고체 상의 Thin Layer를 얻는 방식으로, Precursors의 양과 유동에 따라서 Thin Layer의 Profile이 결정되기 때문에 이들을 세밀히 제어해야 할 필요가 있다. ALD 공정은 Precursors를 Pulse의 형태로 순차적으로 공급한다. 또한 Mono Layer에서 갖는 Chemisorption과 Multi Layers에서 갖는 Physisorption 간의 에너지 차이를 이용하여 Purge 과정에서 Single Layer만 남기는 방식이기 때문에 Precursor의 유동과 양이 상대적으로 낮은 중요성을 갖는다. ALD의 Precursors는 ALD의 공정진행 환경에서 열분해 되지 않아야 하기 때문에, CVD의 경우보다 저온에서 공정이 진행되고 Thermal Stability가 높은 Precursors가 요구된다. 그러나 동시에 Conformal한 성장을 위해서는 ALD의 Precursors는 저온에서도 높은 Reactivity 가져야 한다. 따라서 ALD의 경우는 알맞은 Precursors를 구하는 것이 매우 어렵다.
Q2. 진공 증착에 대해 아는대로 작성해보세요.
진공 증착, 즉 Evaporation은 진공 Chamber 내의 Target 물질을 증발시켜 그 입자를 상부에 위치한 웨이퍼 표면에 증착시키는 방식으로, Uniformity가 PVD나 CVD보다 상대적으로 낮다. 진공증착은 불순물이 혼입될 가능성이 크고 Melting Point가 너무 높은 Target은 증착하기 어렵다. 또한 Alloy의 경우에도 각각의 물질의 Melting Point가 서로 상이하기 때문에 서로 다른 Crucible에서 증발시켜야 하는데, 이렇게 증발된 두 물질은 웨이퍼에서 동일하게 도달하여 증착되어야 하기에 난이도가 매우 어렵다는 단점이 존재한다. 다음과 같은 단점 때문에 Evaporation 공정은 PVD와 CVD로 교체되었다.